In the world of HVAC and refrigeration, refrigerants play a crucial role in cooling and maintaining optimal temperatures. With a variety of refrigerants available, each comes with its own set of characteristics and recovery requirements. Understanding types of refrigerants and their recovery needs is essential for anyone working in the field to ensure proper handling, environmental compliance, and system efficiency.
What Are Refrigerants?
Refrigerants are substances used in refrigeration and air conditioning systems to absorb and release heat. They transition between liquid and gas phases, facilitating the cooling process. The choice of refrigerant can impact system performance, energy efficiency, and environmental impact. Understanding types of refrigerants and their recovery needs becomes critical when deciding which refrigerant is best suited for your HVAC or refrigeration system.
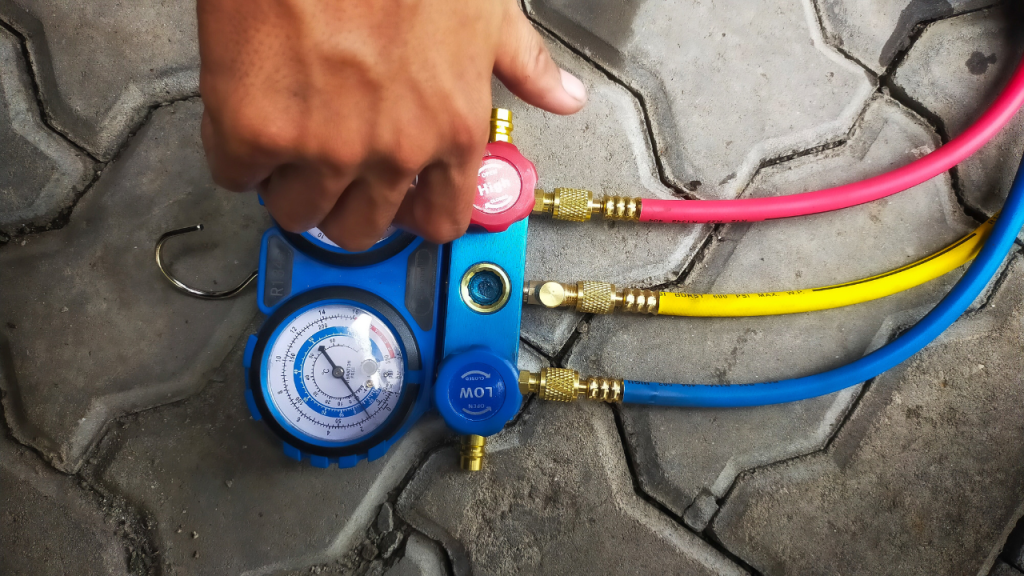
Types of Refrigerants
Refrigerants are typically classified into several categories, each with unique properties and recovery needs:
1. Chlorofluorocarbons (CFCs)
CFCs, such as R-12, were once the go-to refrigerants due to their stability and efficiency. However, they have been largely phased out due to their role in ozone depletion. In systems where CFCs are still in use, recovery and recycling are critical to prevent environmental damage.
Recovery Needs: CFCs must be recovered using specialized equipment designed to handle their high pressures and chemical properties. Proper containment and disposal are crucial to avoid ozone layer damage.
2. Hydrochlorofluorocarbons (HCFCs)
HCFCs like R-22 were introduced as transitional substances with lower ozone depletion potential than CFCs. However, they are still being phased out due to their environmental impact.
Recovery Needs: HCFCs are less harmful to the ozone layer than CFCs but still require careful handling. Recovery involves using appropriate recovery machines and ensuring that any released gases are captured and recycled.
3. Hydrofluorocarbons (HFCs)
HFCs, such as R-134a and R-410A, do not deplete the ozone layer but have high global warming potential (GWP). Their use is being scrutinized and regulated due to their contribution to climate change.
Recovery Needs: HFCs require recovery systems that can handle their pressures and are capable of dealing with their impact on global warming. These refrigerants must be recovered, recycled, or destroyed following regulations to mitigate their environmental impact.
4. Hydrofluoroolefins (HFOs)
HFOs like R-1234yf are newer refrigerants designed to offer lower GWP and reduced environmental impact compared to HFCs. They are increasingly being used in newer systems.
Recovery Needs: While HFOs are less harmful to the environment, they still require proper recovery techniques. Equipment used for HFOs must be compatible with their chemical properties and pressures. Efficient recovery practices help ensure their benefits are fully realized.
5. Natural Refrigerants
Natural refrigerants, including ammonia (R-717), carbon dioxide (R-744), and hydrocarbons (such as propane R-290), offer low environmental impact and excellent performance. They are becoming more popular as alternatives to synthetic refrigerants.
Recovery Needs: Each natural refrigerant has unique recovery requirements. For instance, ammonia requires careful handling due to its toxicity, while CO2 operates at high pressures. Recovery systems must be designed to manage these specific needs safely.
Recovery and Recycling Practices
Regardless of the type of refrigerant, proper recovery and recycling are essential for environmental protection and compliance with regulations. Here are some best practices:
- Use Proper Equipment: Ensure recovery machines are designed for the specific refrigerant type, handling its pressures and properties safely.
- Follow Regulations: Adhere to local and international regulations regarding refrigerant recovery and disposal. The Environmental Protection Agency (EPA) in the U.S. and similar agencies worldwide set standards for refrigerant management.
- Training and Certification: Technicians should be trained and certified in refrigerant handling and recovery to ensure safe and effective practices.
- Leak Detection: Regularly inspect and maintain systems to prevent leaks, which can lead to refrigerant loss and environmental harm.
Conclusion
Understanding the different types of refrigerants and their recovery needs is crucial for maintaining system efficiency and protecting the environment. As technology advances and regulations evolve, staying informed and adopting best practices will help ensure that refrigerant handling is done responsibly and effectively. Whether dealing with legacy refrigerants or the latest alternatives, proper recovery and recycling are essential steps in minimizing environmental impact and supporting sustainable practices in the HVAC and refrigeration industry.
Refrigerant Services LLC
54000 Grand River Ave
New Hudson, MI 48165
#844-PURE-CFC (787-3232)
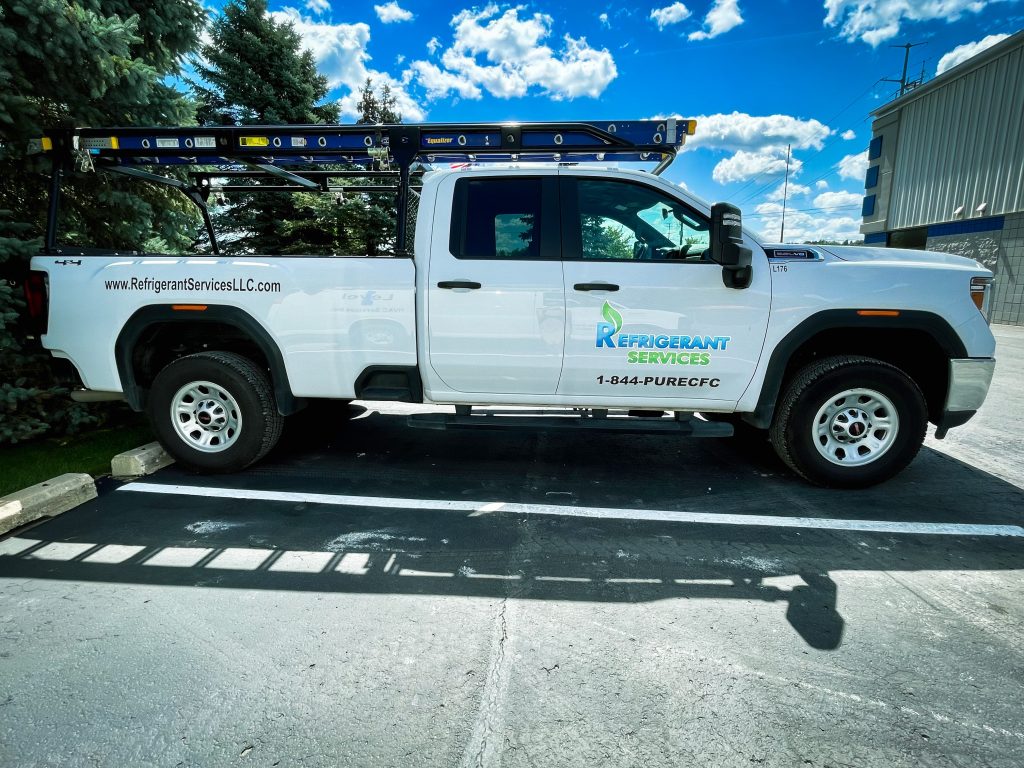